机械制造技术课程设计-接头加工工艺规程及其车夹具设计.docx
《机械制造技术课程设计-接头加工工艺规程及其车夹具设计.docx》由会员分享,可在线阅读,更多相关《机械制造技术课程设计-接头加工工艺规程及其车夹具设计.docx(23页珍藏版)》请在优知文库上搜索。
1、第一章零件的分析第二章工艺规程的设计22.1确定毛坯的的制造形式22.2基的选择.*22.3制订工艺路线22. 3.1工艺路线方案一,23. 3.2工艺路线方案二34. 3.3工艺方案的分析32. 4机械加工余量的确定42.5确定切削用量及基本工时4第三章专用夹具的设计143. 1问题的提出143 .2定位基准的选择144 .3切削力及夹紧力计算153. 3.1切屑力】卜夕;。153. 3.2夹紧力的计算153. 4/E(/J天差分析1635彳vt17偏土.2122第一章零件的分析接头的加工共有二组加工表面,它们相互之间没有要求。现分述如下:1、以35x65面为中心的加工面,这组面包括:35X
2、65面,2-5.2孔。2、以24圆为中心的加工面,这组面包括:中24端面及其外圆面,8孔和2-e5.2孔有以上的分析可知,对于这两组加工表面而言,可以先加工其中一组表面,然后借助于夹具加工另一组表面,并保证它们的图1-1接头零件图第二章工艺规程的设计2.1 确定毛坯的的制造形式零件材料为ZG25。接头在使用过程中经常的变动,它不仅起压紧的作用,还又摆动的作用,受到的冲击很大。在加工过程中的精度保证很重要,它对工件的定位有一定的保证作用。2.2 基准的选择1 .粗基准的的选择根据粗基准的选择原则,要亦非加工表面为粗基准,且粗基准只能使用一次,对本工件来说选择24外圆面为粗基准是非常合理的。2.精
3、基准的选择主要考虑的是基准的中和问题。当设计与工序的基准不重合时,因该进行尺寸换算。以直径为5.2的两孔作为精基准以35x65面作为辅助基准。2.3 制订工艺路线2.3.1 工艺路线方案一工序01:锻造工序02:退火工序03:粗铳,精铳35x65表面,粗糙度为3.2工序04;钻,扩面35x65上2-5.2孔,粗糙粗6.3工序05:车,精车中24端面和外圆,粗糙度3.2工序06:钻,扩中8孔和2-中5.2孔,粗糙度6.32.3.2 发蓝处理2.3.3 检验,入库2.3.4 工艺路线方案二工序01:锻造工序02:退火工序03:粗铳,精铳35x65表面,粗糙度为3.2工序04;车,精车中24端面和外
4、圆,粗糙度3.2工序05:钻,扩面35x65上2-5.2孔,粗糙粗6.3工序06:钻,扩中8孔和2-5.2孔,粗糙度6.3工序07:发蓝处理工序08:检验,入库2.3.5 工艺方案的分析上述两个工艺方案的特点在于:方案二是先加工所有的面,然后加工所有孔。方案一则是先加工35x65面,然后再加工这个面上的圆孔,这样用这个面上加工的孔定位。加工其它的面和孔,很好的保证了精度,经比较可知,显然方案一比方案二的装夹次数减少了,同时也更好的保证了精度要求。具体的工艺过程如下:工序01:锻造工序02:退火工序03:粗铳,精铳35x65表面,粗糙度为3.2工序04;钻,扩面35x65上2-5.2孔,粗糙粗6
5、.3工序05:车,精车中24端面和外圆,粗糙度3.2工序06:钻,扩中8孑L和2-中5.2孑L,粗糙度6.3工序07:发蓝处理工序08:检验,入库2.4 机械加工余量的确定“接头”零件材料为ZG25,毛坯的重量约为1.2Kg,生产类型为大批量生产,采用砂型机铸造毛坯。1、不加工表面毛坯尺寸不加工表面毛坯按照零件图给定尺寸为自由度公差,由铸造可直接获得。2、接头的35x65面由于接头3565面要与其他接触面接触,粗糙度要求为3.2,查相关资料知余量留2.O比较合适。3、接头的孔毛坯为实心。孔的精度要求介于IT9mi之间。2.5 确定切削用量及基本工时工序01:锻造工序02:退火处理工序03:粗铳
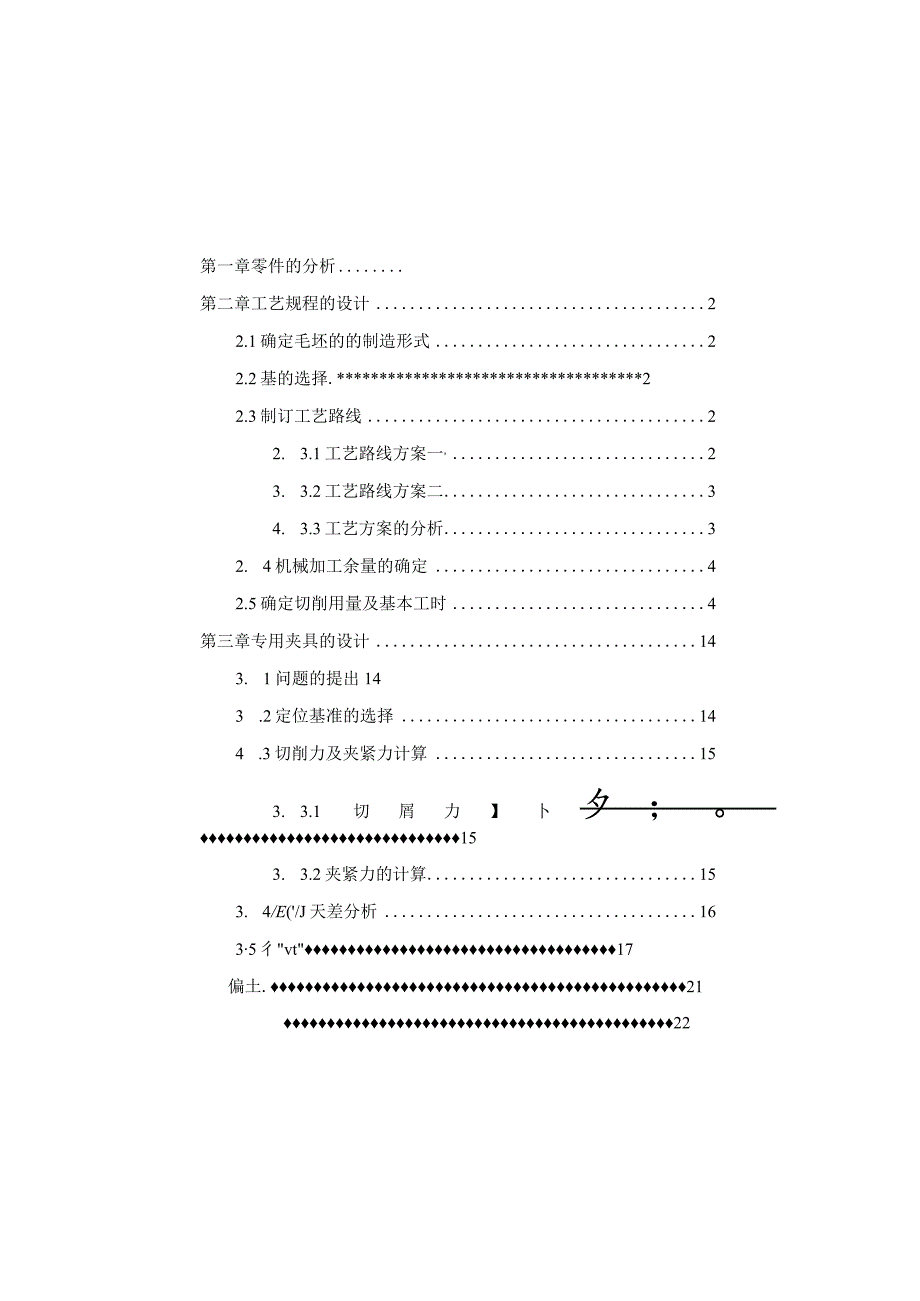
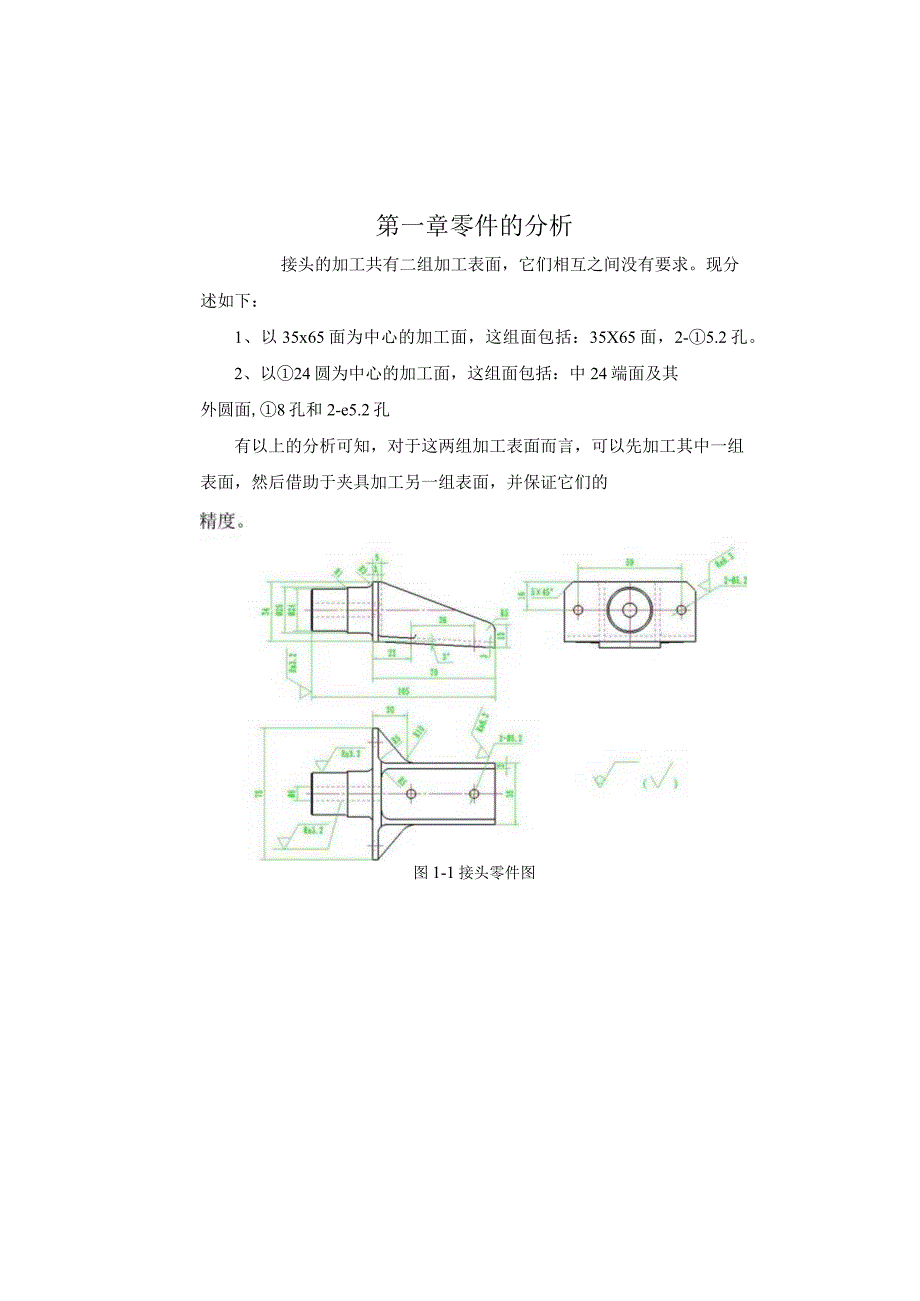
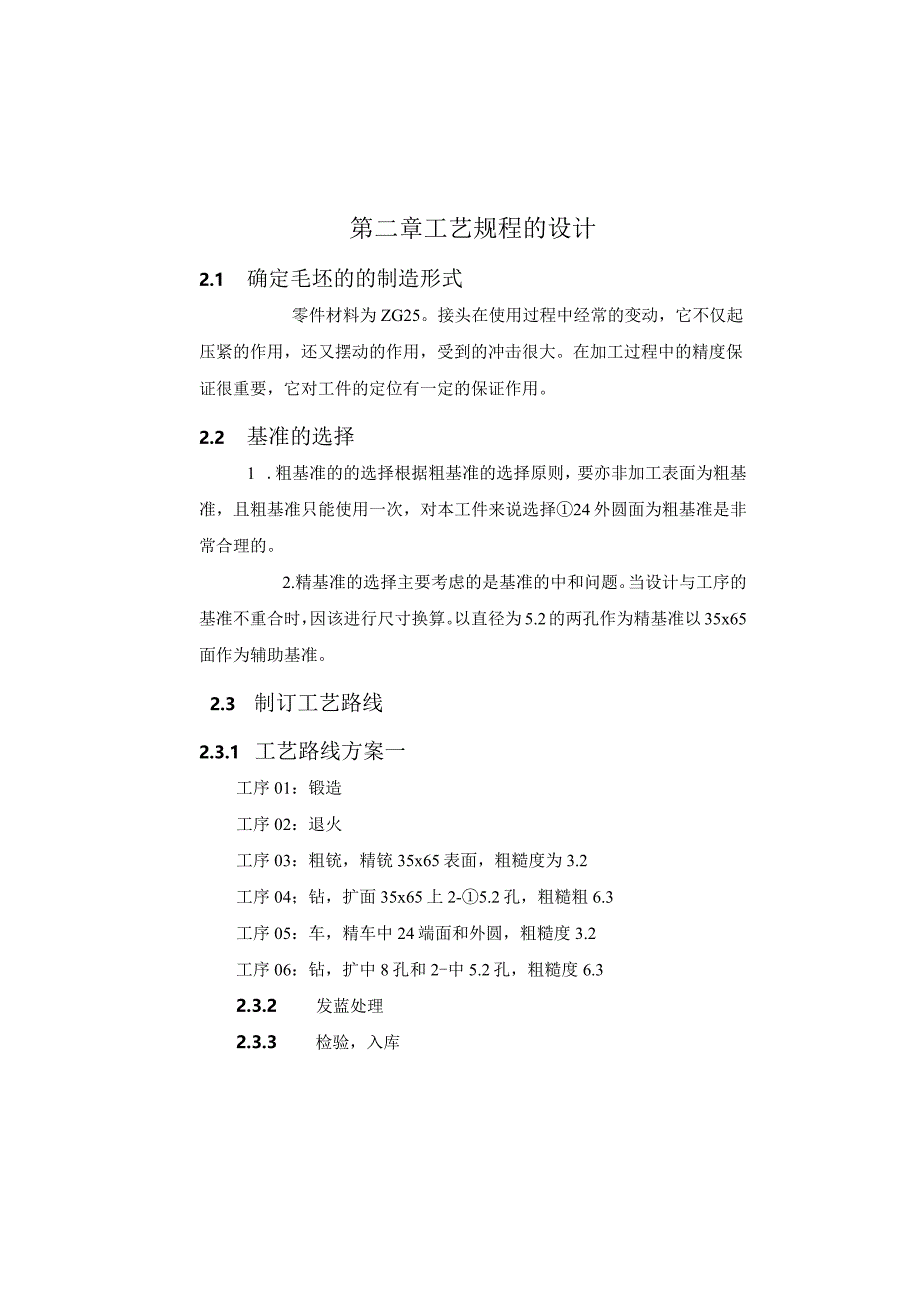
- 配套讲稿:
如PPT文件的首页显示word图标,表示该PPT已包含配套word讲稿。双击word图标可打开word文档。
- 特殊限制:
部分文档作品中含有的国旗、国徽等图片,仅作为作品整体效果示例展示,禁止商用。设计者仅对作品中独创性部分享有著作权。
- 关 键 词:
- 机械制造 技术 课程设计 接头 加工 工艺 规程 及其 夹具 设计
