危险源辨识及分级管控管理制度.docx
《危险源辨识及分级管控管理制度.docx》由会员分享,可在线阅读,更多相关《危险源辨识及分级管控管理制度.docx(28页珍藏版)》请在优知文库上搜索。
1、危险源辨识及分级管控管理制度1 目的为加强安全管理,消除或减少危害,辩识、评价生产、经营过程、活动中的健康、安全危害因素并提前采取预防措施,有效遏制重特大生产安全事故,特制定本制度。2 适用范围本制度适用于公司的所有部门的所有活动,包括生产活动、设备设施、原料产品、安全防护、正常和异常活动、人为因素、违反操作规程和管理制度等安全风险的辨识、评价分级和控制管理。3 职责3.1 各部门a)识别和评价管理范围内危险源;b)制定危险源的控制措施;c)管理范围内危险源的控制。3.2 安环部a)汇总评价各部门提报的危险源,确定公司危险源清单并进行分类;b)组织制定重大危险源的控制措施;C)监视检查危险源的
2、控制状况;d)跟踪验证所制定的控制措施的实施。4 风险评价准则风险分级管控原则如下:3.3 A级:红色风险不可容许的(巨大风险),极其危险,必需当即整改,不能继续作业。该风险点一旦发生事故,可能导致较大以上事故,即3人以上死亡,或者10人以上重伤,或者1000万元以上直接经济损失的事故;3.4 B级:橙色风险高度危险(重大风险),必需制定措施进行控制管理.该风险点一旦发生发生事故,可能导致一般事故,即指能造成3人以下死亡,或者10人以下重伤,或者1000万元以下直接经济损失的事故。3.5 C级:黄色风险中度(显著)危险,需要控制整改。该风险点一旦发生发生事故,可能导致轻伤事故(包括急性工业中毒
3、,下同)或微弱经济损失。3.6 D级:蓝色风险轻度(一般)危险,可以接受(或可容许的).指该风险点一旦发一事故,可能导致不损失工作日伤害。3.7 以下情形应直接确定为B级风险:(1)开停车作业、非正常工况的操作;(2)同一-爆炸危险区域内,现场作业人员10人以上的;(3)10人以上的检维修作业及特别作业;3.8 风险控制措施计划对4个级别的风险实施多种措施控制:A级红色风险,B级橙色风险,C级黄色风险,D级蓝色风险。公司应依次依照工程控制措施、安全管理措施、个体防护措施以应急措施等四个规律顺序对每个风险点制定精准的风险控制措施.5 风险点识别和评价方法经研究公司决定以安全检查表法(SCL)对生
4、产现场及其它区域的物的担忧全状态、作业环境担忧全因素及管理缺陷进行识别;以作业危害分析法(JHA)并依照作业步骤分解逐一对作业过程中的人的担忧全行为进行识别。风险评价方法采用风险矩阵法(L-S)进行风险评价。5.1 作业风险分析法(风险矩阵)作业风险分析方法(风险矩阵),英国石油化工行业最先采用.就是识别出每个作业活动可能存在的危害,并判定这种危害可能产生的后果及产生这种后果的可能性,二者相乘,得出所确定危害的风险.然后进行风险分级,根据不同级别的风险,采取相应的风险控制措施。风险的数学表达式为:R=LXS.其中:R一代表风险值;1.一代表发生伤害的可能性;S代表发生伤害后果的严重程度。赋值偏
5、差发生频率安全检查操作规程员工胜任程度(意识、技能、经验)控制措施(监控、联锁、报警、应急措施)5每次作业或每月发生无检查(作业)标准或不按标准检查(作业)无操作规程或从不执行操作规程不胜任(无上岗资格证、无任何培训、无操作技能)无任何监控措施或有措施从未投用;无应急措施.4每季度都有发生检查(作业)标准不全或很少按标准检查(作业)操作规程不全或很少执行操作规程不够胜任(有上岗资格证、但没有接受有效培训、操作技能差)有监控措施但不能满足控制要求,措施部分投用或有时投用;有应急措施但不完善或没演练.3每年都有发生发生变更后检查(作业)标准未及时修订或多数时候不按标准检查(作业)发生变更后未及时修
6、订操作规程或多数操作不执行操作规程一般胜任(有上岗资格证、接受培训、但经验、技能不足,曾屡屡出错)监控措施能满足控制要求,但经常被停用或发生变更后不能及时恢复;有应急措施但未根据变更及时修订或作业人员不明白。2每年都有发生或曾经发生过标准完善但偶尔不按标准检查、作业操作规程齐全但偶尔不执行胜任(有上岗资格证、接受有效培训、经验、技能较好,但偶尔出错)监控措施能满足控制要求,但供电、联锁偶尔失电或误动作;有应急措施但每年只演练一次。I从未发生过标准完善、按标准进行检查、作业操作规程齐全,严格执行并有记录高度胜任(有上岗资格证、接受有效培训、经验丰富,技能、安全意识强)监控措施能满足控制要求,供电
7、、联锁从未失电或误动作;有应急措施每年至少演练二次。Co1事故发生的可能性(L)取值对照表C。1从偏差发生频率、安全检查、操作规程、员工胜任程度、控制措施五个方面对危害事件发生的可能性进行评价取值,取五项得分的最高的分值作为其最终的L值。5.2 危害事件发生的严重程度(三)等级人员伤害状况财产损失、设备设施损坏法律法规符合性环境破坏声誉影响1一般无损伤一次事故直接经济损失在5000元以下完全符合基本无影响本岗位或作业点21至2人轻伤一次事故直接经济损失5000元及以上,1万元以下不符合公司规章制度要求设备、设施周边受影响没有造成公众影响3造成1至2人重伤3至6人轻伤一次事故直接经济损失在1万元
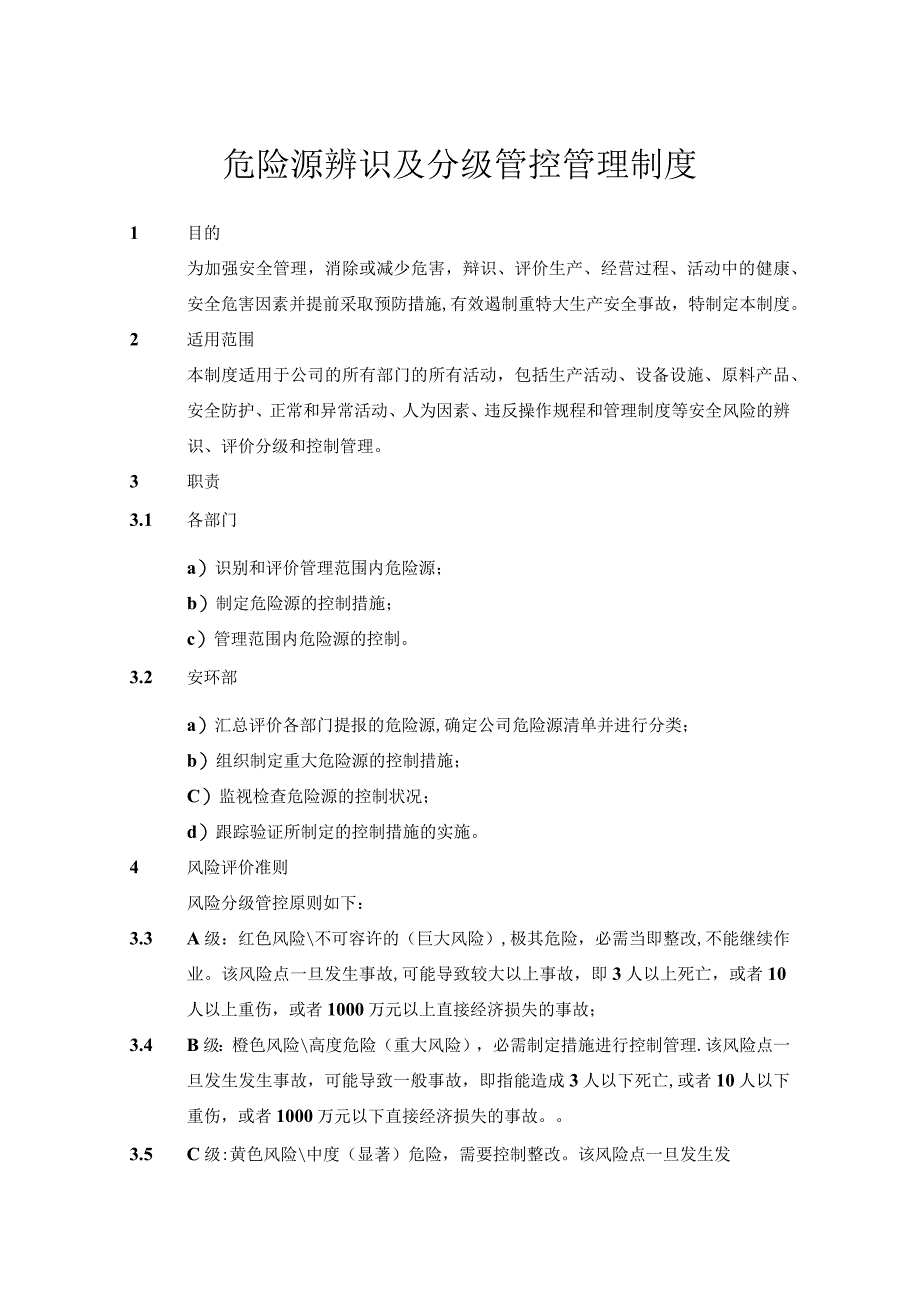
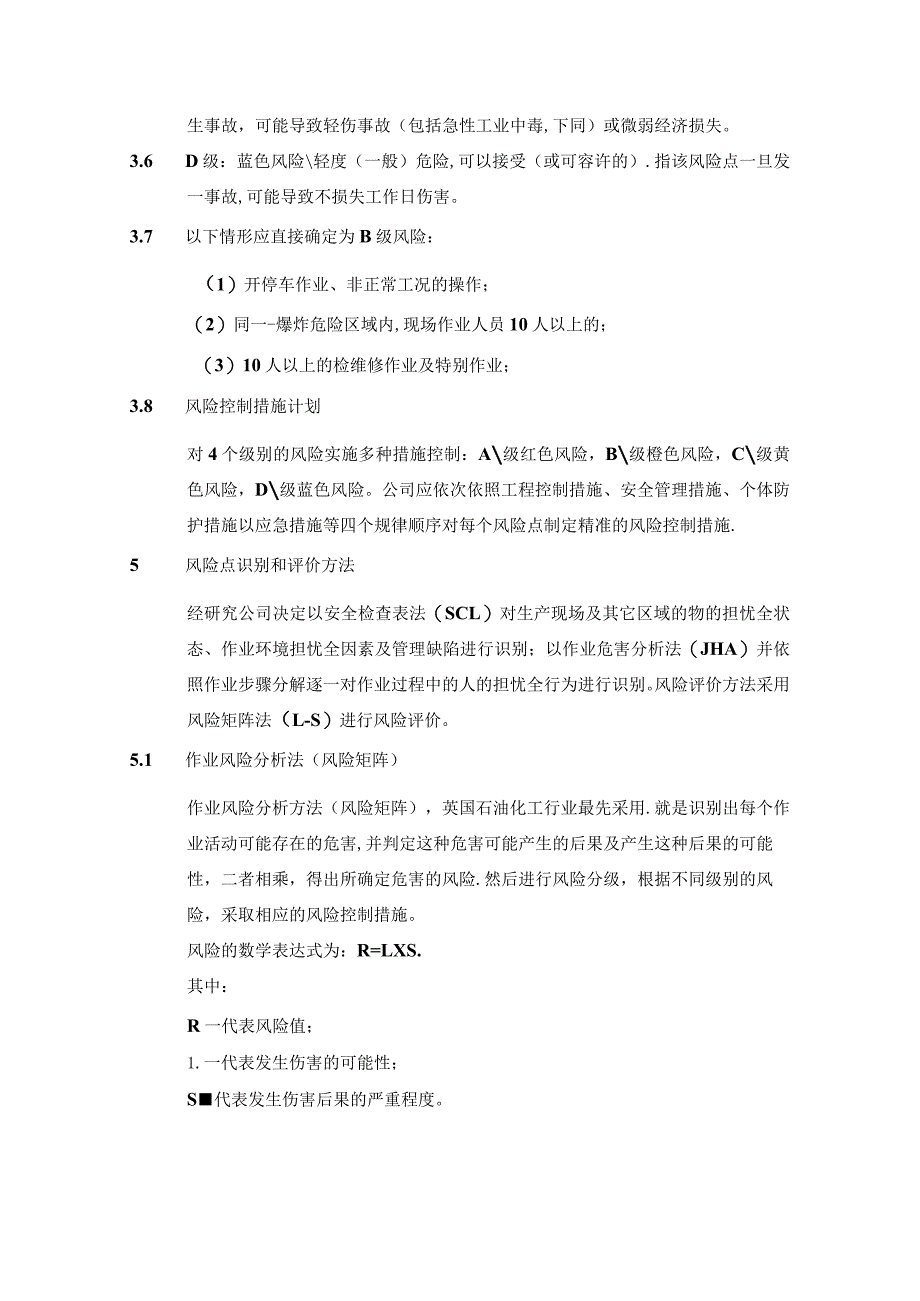
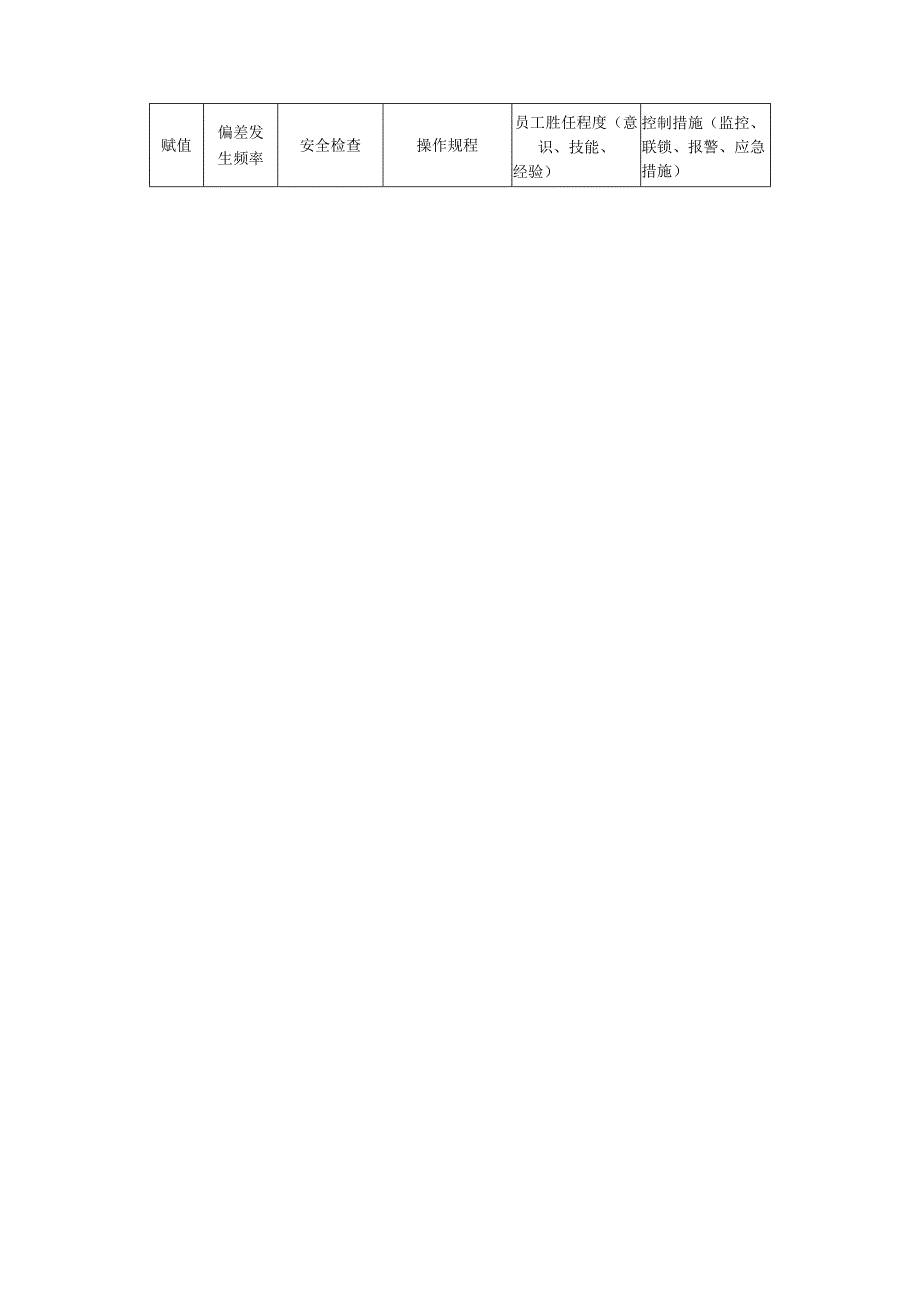
- 配套讲稿:
如PPT文件的首页显示word图标,表示该PPT已包含配套word讲稿。双击word图标可打开word文档。
- 特殊限制:
部分文档作品中含有的国旗、国徽等图片,仅作为作品整体效果示例展示,禁止商用。设计者仅对作品中独创性部分享有著作权。
- 关 键 词:
- 危险源 辨识 分级 管理制度
