焊后自动测量自动矫形方案说明.docx
《焊后自动测量自动矫形方案说明.docx》由会员分享,可在线阅读,更多相关《焊后自动测量自动矫形方案说明.docx(3页珍藏版)》请在优知文库上搜索。
1、焊后自动测量自动矫形方案1.适用范围本方案适用于挖机结构件的焊后自动测量自动矫形。2 .系统构成及功能描述2.1 三维激光扫描设备:使用高精度三维激光扫描仪对焊接后的结构件进行全面扫描,获取其表面几何形状的精确数据。将扫描数据与原始设计模型进行对比分析,计算出焊后变形的具体数值和位置。完成矫形后再次使用三维扫描系统进行复测,确保结构件达到设计要求的精度标准。2.2 数据处理系统:根据扫描结果生成三维可视化模型,识别并量化变形区域的尺寸偏差。确定需要矫正的位置及其对应的矫正量。2.3 机器人矫形系统:配备工业机器人(如六轴机械臂),并在末端安装专用矫形工具(如液压顶推器、热矫形设备等)。根据测量
2、得到的数据,通过控制系统编程实现对各个变形点的精准定位和力矩控制。2.4 智能控制系统:控制系统接收测量系统的偏差数据,并根据预设算法制定矫形策略。实时监控矫形过程,动态调整矫形力度和角度,确保在不破坏材料性能的前提下完成矫形任务。3 .先进性描述采用三维激光扫描测量等先进技术,能够对复杂几何形状和大型结构件实现毫米级甚至更高精度的全面无接触测量,大大提高了焊后变形检测的准确度和效率。令将CAD模型与实际焊接后的部件进行对比分析,实现从设计到生产再到质量控制的全链条数字化管理,有助于提高产品质量及一致性。集成了机器人技术和精确控制系统,可以针对测量结果自动生成矫形策略,并由机器人执行精细化操作
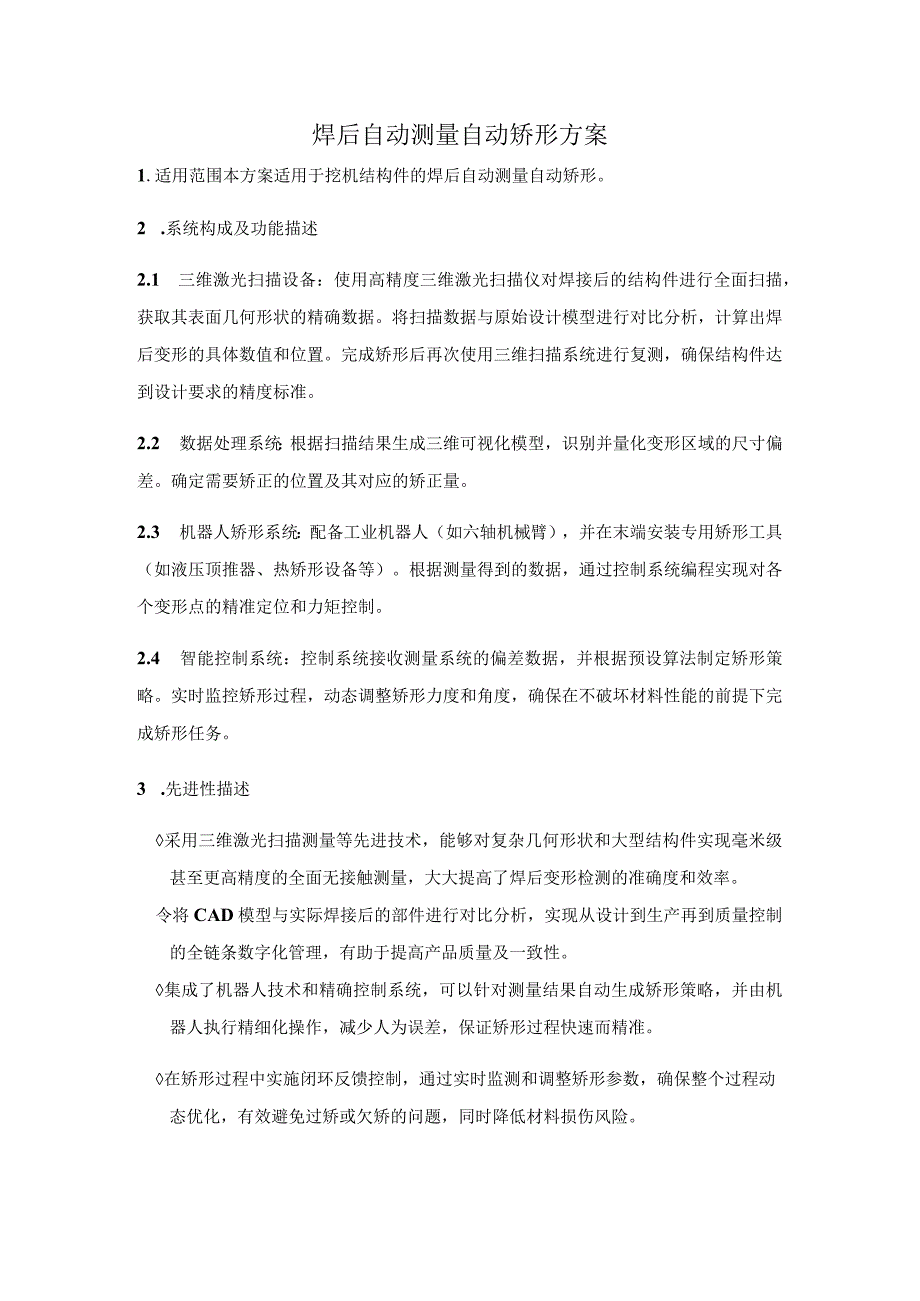
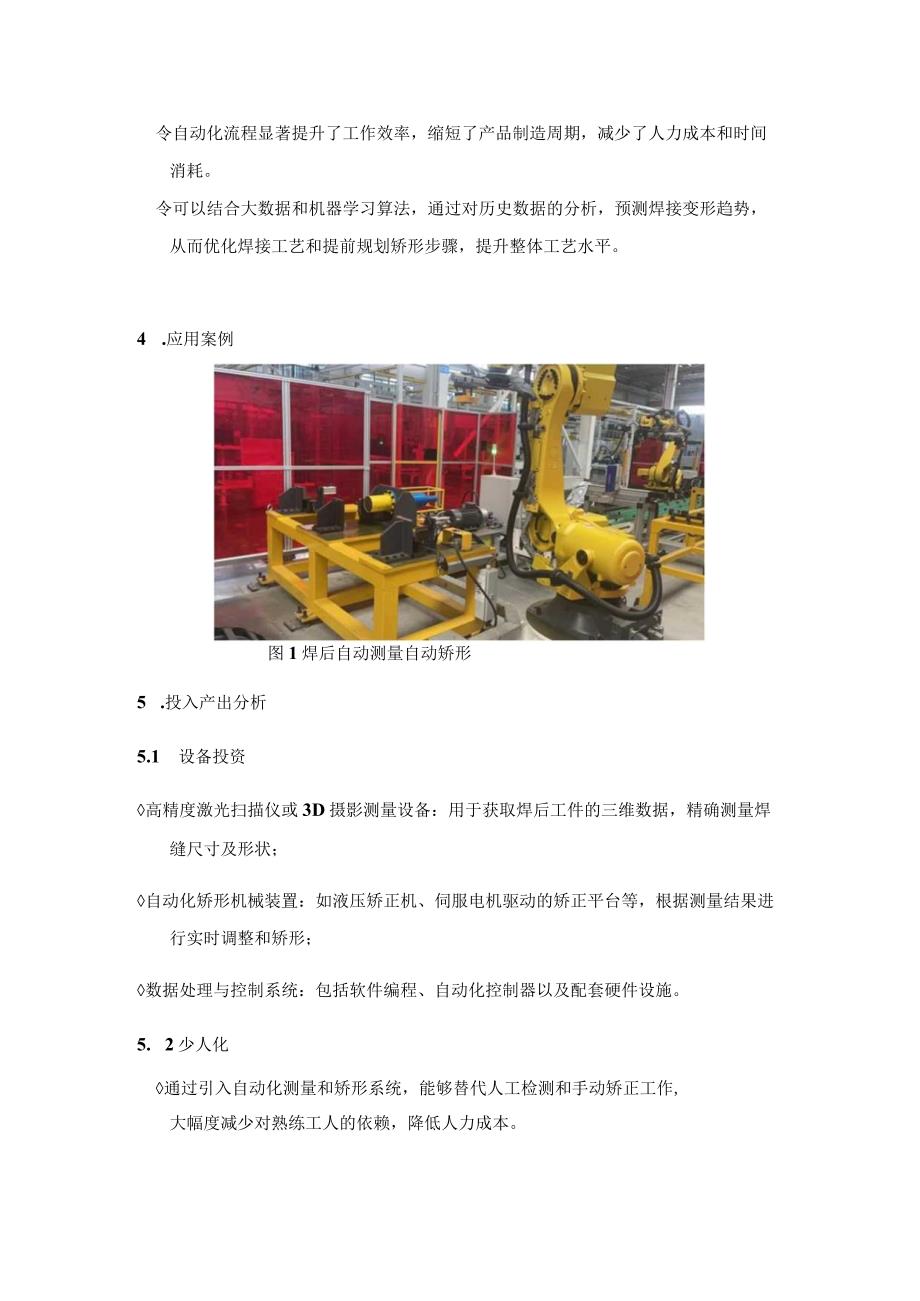
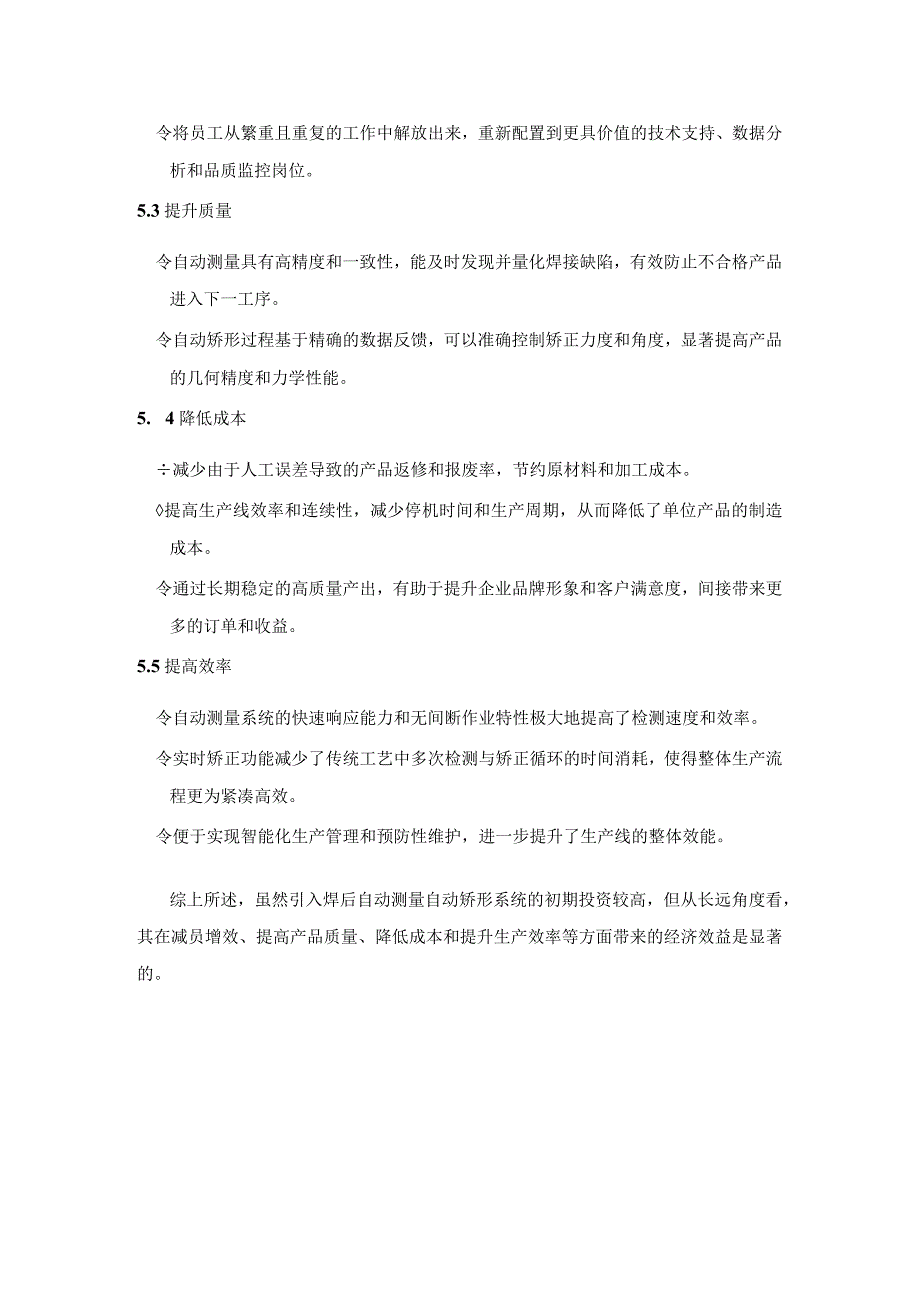
- 配套讲稿:
如PPT文件的首页显示word图标,表示该PPT已包含配套word讲稿。双击word图标可打开word文档。
- 特殊限制:
部分文档作品中含有的国旗、国徽等图片,仅作为作品整体效果示例展示,禁止商用。设计者仅对作品中独创性部分享有著作权。
- 关 键 词:
- 自动 测量 矫形 方案 说明
